Information about lubrication grease
Packaging
Lubrication grease is available in different packaging format. Our grease equipment can be used for:
• 12-20 kg plastic or metal container
• 60 kg metal drum (sometimes called ¼ drum)
• 180 kg metal drum (sometimes called 1/1 drum)
• 1000 kg grease fluid bag
• 12-20 kg plastic or metal container
• 60 kg metal drum (sometimes called ¼ drum)
• 180 kg metal drum (sometimes called 1/1 drum)
• 1000 kg grease fluid bag
Lubricating grease purpose
Lubrication grease is basically a lubrication oil that has been mixed with a thickener (soap) that will keep the oil in its place (not floating out). Grease usually also contain special additives that will improve its properties like: load capacity, friction coefficient, wear and corrosion protection etc.
Lubrication grease minimize the wear on moving parts. When friction is reduced in engines and machines they run more efficiently. Grease also protects parts from corrosion and is designed to be active during a long lime.
Greases are divided into groups by their usage and corresponding soap type. Greases
that are marked with EP (Extreme Pressure) have additives that will make them handle exposed parts during high pressure load.
NLGI describes the lubrication grease by its rate of penetration. Test standard is that a certified cone is dropped down in the grease, whereas the drop down distance is measured in 1/10 mm. The result is by this given the penetration rate number, correlating with a table listing NLGI numbers. The NLGI scale start at 000 (very soft consistency) to 6 (very hard).
Lubrication grease minimize the wear on moving parts. When friction is reduced in engines and machines they run more efficiently. Grease also protects parts from corrosion and is designed to be active during a long lime.
Greases are divided into groups by their usage and corresponding soap type. Greases
that are marked with EP (Extreme Pressure) have additives that will make them handle exposed parts during high pressure load.
NLGI describes the lubrication grease by its rate of penetration. Test standard is that a certified cone is dropped down in the grease, whereas the drop down distance is measured in 1/10 mm. The result is by this given the penetration rate number, correlating with a table listing NLGI numbers. The NLGI scale start at 000 (very soft consistency) to 6 (very hard).
Pipes used for grease
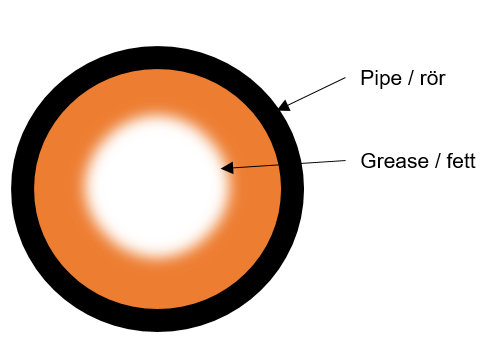
Pipes:
Ø20 x 3 mm: 0 - 20 m
Ø25 x 3 mm: 0 - 35 m
Ø38 x 4 mm: 0 - 60 m
Hoses:
ؼ” 0 – 10 m: Steel braided hose 3-layers
Ø⅜” 0 – 15 m: Steel braided hose 3-layers
ؽ” 0 – 20 m: Steel braided hose 3-layers
Choosing the right pump
Standard grease of NLGI 1-2
In most standard applications pump ratios of 55:1 to 60:1 are used. Our 60:1 pump has a higher pumping capacity and usually works well in both mobile and in stationary applications.
12750: pump for 12-20 kg containers
12751: pump for 60 kg drum (1/4-drum)
12752: pump for 180 kg drum (1/1-drum)
Very adhesive (sticky) greases and/or when pump is operating very frequently.
In these cases it is recommended to use a pump with a separated air motor from the pump tube. These pumps are made/used to avoid that grease reach their air motors.
Very sticky grease has a high adhesion bond to the piston rod and thereby seep through seals. When this small amount of grease reach the air motor it will cool down (from air pressure inside the air motor) and make it even stiffer. Some of the grease coating will then be scraped off inside the air motor.
The same may also occur when air operated pumps are running for long periods, due to the high cooling effect.
Grease pump 60:1 (with separated air motor)
12650: pump for 12-20 kg containers
12651: pump for 60 kg drum (1/4-drum)
12652: pump for 180 kg drum (1/1-drum)
Grease pump 80:1
Used when available air pressure is in the low range of 3-4 bar
12755: pump for 12-20 kg container
12756: pump for 60 kg drum (1/4-drum)
12757: pump for 180 kg drum (1/1-drum)
Grease pumps for industrial use (heavy duty)
When pumping larger volume of grease or using a longer pipe system we recommend to use below pump series:
1282x
1283x
1284x
These heavy duty pumps are equipped with air piston diameters of 4 ½” or 6” and a pressure ratio range from 12:1 to 80:1. Due to their weight and capacity they are usually installed with a pump lifting device like our one & two post ram systems.
An important note is to make sure that air supply is adequate for these heavy duty pumps.
In most standard applications pump ratios of 55:1 to 60:1 are used. Our 60:1 pump has a higher pumping capacity and usually works well in both mobile and in stationary applications.
12750: pump for 12-20 kg containers
12751: pump for 60 kg drum (1/4-drum)
12752: pump for 180 kg drum (1/1-drum)
Very adhesive (sticky) greases and/or when pump is operating very frequently.
In these cases it is recommended to use a pump with a separated air motor from the pump tube. These pumps are made/used to avoid that grease reach their air motors.
Very sticky grease has a high adhesion bond to the piston rod and thereby seep through seals. When this small amount of grease reach the air motor it will cool down (from air pressure inside the air motor) and make it even stiffer. Some of the grease coating will then be scraped off inside the air motor.
The same may also occur when air operated pumps are running for long periods, due to the high cooling effect.
Grease pump 60:1 (with separated air motor)
12650: pump for 12-20 kg containers
12651: pump for 60 kg drum (1/4-drum)
12652: pump for 180 kg drum (1/1-drum)
Grease pump 80:1
Used when available air pressure is in the low range of 3-4 bar
12755: pump for 12-20 kg container
12756: pump for 60 kg drum (1/4-drum)
12757: pump for 180 kg drum (1/1-drum)
Grease pumps for industrial use (heavy duty)
When pumping larger volume of grease or using a longer pipe system we recommend to use below pump series:
1282x
1283x
1284x
These heavy duty pumps are equipped with air piston diameters of 4 ½” or 6” and a pressure ratio range from 12:1 to 80:1. Due to their weight and capacity they are usually installed with a pump lifting device like our one & two post ram systems.
An important note is to make sure that air supply is adequate for these heavy duty pumps.
Accessories for grease pumps
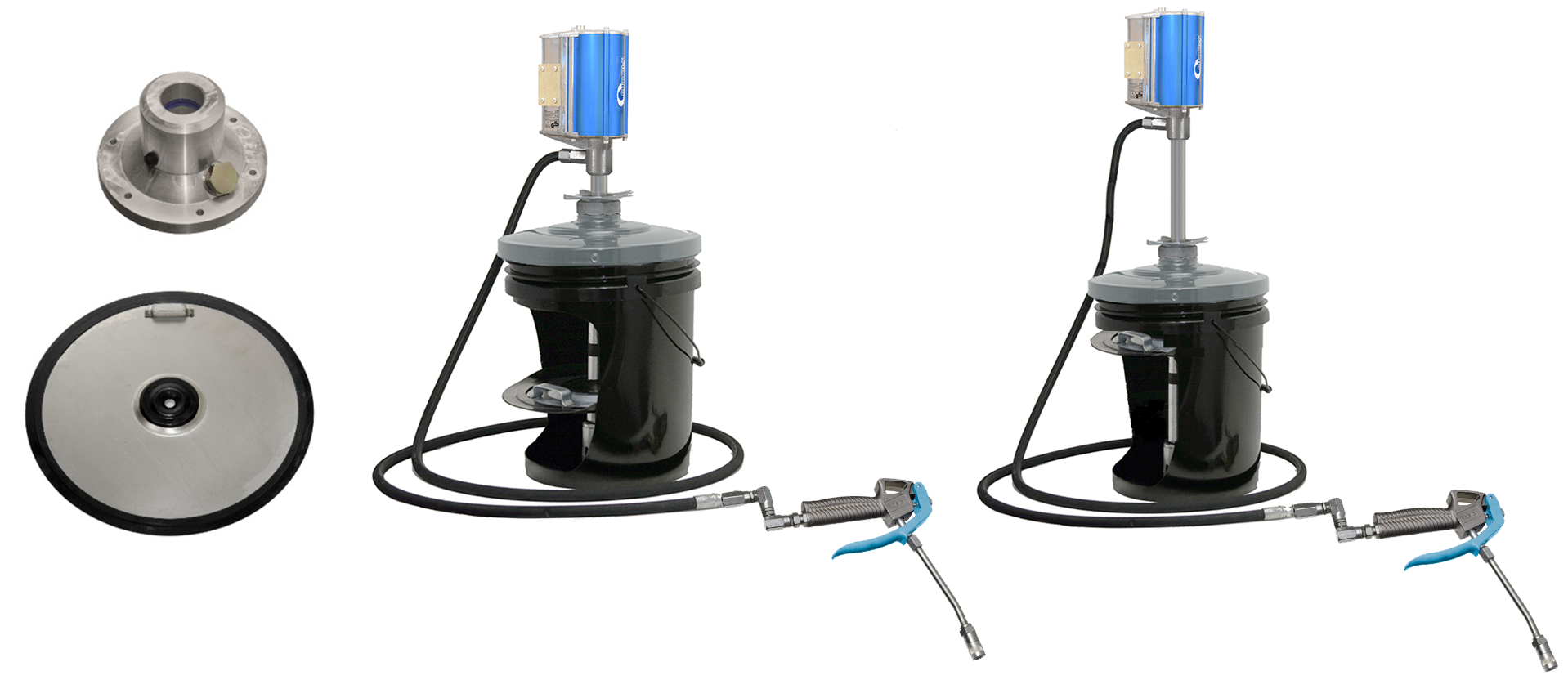
Using a follower plate prevents that air pockets develops in grease, but it also improves the grease feeding to the pump. The rubber flange of the plate wipes off the grease from the drum wall. It will also prevent that dirt will reach the grease (get trapped onto/into it) and then fed to the pump, but also moving further (causing larger problems).
The follower plate adapter is used to further improve the clearance of the drum. The adapter is mounted on the follower plate and then mounted over the pump tube (that is secured by the adapter screw). The weight of the pump with the mounted follower plate will push the grease down as the pump operates (as vibrations will assist).
Using this assembly kit will also make it easy to see how much grease is left in a drum (by the pump height reference). An important note is that our follower plates are not supplied with screw holes, but need to be prepared/drilled by the user (and then also mounted).
The follower plate adapter is used to further improve the clearance of the drum. The adapter is mounted on the follower plate and then mounted over the pump tube (that is secured by the adapter screw). The weight of the pump with the mounted follower plate will push the grease down as the pump operates (as vibrations will assist).
Using this assembly kit will also make it easy to see how much grease is left in a drum (by the pump height reference). An important note is that our follower plates are not supplied with screw holes, but need to be prepared/drilled by the user (and then also mounted).
Handling of grease pumps are of the highest importance
Grease pumps are more than often placed on the floor during the drum change. This is very risky as dirt/sand etc. will stick to the grease coated pump. These particles will then easily get inside it and cause damage/problems (also at the end of the line as contaminated grease is not good for machines). This is the single most known problem related to claims on grease pumps.
To avoid above mentioned problems it is recommended to use pump hoists/lifts and ram posts. These devices will also make it easier to handle uneven drums (as a basic follower plate may get stuck inside it without the assisting device).
If the grease drum is fitted with an internal plastic bag it is recommended to be securely strapped around the drum before the follower plate is pushed down in the grease.
To avoid above mentioned problems it is recommended to use pump hoists/lifts and ram posts. These devices will also make it easier to handle uneven drums (as a basic follower plate may get stuck inside it without the assisting device).
If the grease drum is fitted with an internal plastic bag it is recommended to be securely strapped around the drum before the follower plate is pushed down in the grease.